All Concerning Packaging Equipment Repair Work Providers: Important Insights for Preserving Your Machinery
Packaging tools repair services play an important function in the production procedure. They assure that equipment runs efficiently and produce consistent results. Normal maintenance and prompt fixings can conserve organizations from pricey downtimes. Nevertheless, many operators ignore the indicators that show a demand for fixing. Comprehending these signs and knowing just how to choose the right provider can substantially affect a business's performance and bottom line. What should services focus on to guard their procedures?
Comprehending the Value of Packaging Equipment Repair
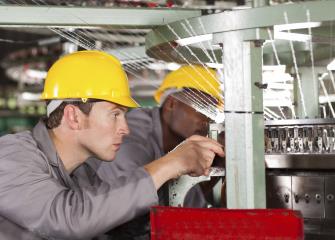
Usual Signs Your Equipment Demands Repair
Recognizing the indicators that packaging tools requires fixing is essential for keeping operational efficiency. Usual indicators consist of unusual noises throughout procedure, lowered manufacturing performance, and constant jams or errors. Recognizing these concerns early can prevent more damage and costly downtime.
Unusual Sounds Throughout Operation
Uncommon sounds throughout operation can function as vital indications that packaging equipment needs repair service. Such noises may include grinding, clanking, or high-pitched whining, which usually recommend underlying mechanical concerns. As an example, grinding sounds may indicate misaligned components or used bearings, while clanking sounds might indicate loose components or international items obstructing the machinery. High-pitched yawping might suggest troubles with the motor or drive systems. Overlooking these noises can lead to more considerable damages and pricey repair work. Regular upkeep checks are necessary to recognize and resolve these acoustic warnings without delay. Operators must preserve an eager understanding of their tools's noises, as very early detection of unusual noises can avoid long term downtime and enhance the longevity of the machinery.
Lowered Manufacturing Performance
Lowered production performance commonly signals that product packaging tools requires fixing. When equipment runs listed below its perfect ability, it can result in significant delays and reduced output. This decline may materialize as longer cycle times or a lack of ability to meet manufacturing targets. Operators could see a decrease in the rate at which products are packaged or filled, indicating possible problems within the equipment. Additionally, a constant failure to preserve well-known efficiency metrics can further highlight underlying problems. Disregarding these signs can result in greater functional losses and higher prices. Because of this, timely analysis and fixing of the equipment are vital to recover efficiency and warranty that manufacturing processes remain effective and structured. Routine maintenance checks can aid preemptively resolve these concerns.
Frequent Jams or Errors
Often, product packaging equipment might show indications of breakdown through functional errors or consistent jams. These issues can interrupt operations and result in considerable downtime. Typical sources of frequent jams consist of damaged parts, imbalance, or particles obstructing the equipment. Operational errors, on the other hand, could originate from software program problems, wrong settings, or not enough upkeep. Recognizing these signs early is vital for stopping further damages and making sure constant production quality. Routine evaluations can assist identify prospective problems prior to they intensify. Resolving frequent jams or mistakes without delay can save suppliers money and time, inevitably improving total efficiency. Therefore, timely repair services are vital to keep peak performance and extend the lifespan of packaging tools.
Preventative Upkeep Techniques
Preventative upkeep approaches are important for guaranteeing the longevity and effectiveness of product packaging devices. Executing arranged upkeep intervals, conducting regular inspections, and using proper lubrication and cleansing techniques can substantially decrease the chance of unforeseen breakdowns. These techniques not only enhance devices efficiency but additionally optimize functional performance.
Set Up Upkeep Intervals
Set up maintenance intervals play a necessary duty in making certain the long life and effectiveness of packaging devices. By establishing a regular maintenance timetable, firms can proactively deal with prospective problems before they rise right into expensive repairs or downtime. These intervals ought to be customized to the specific machinery and its functional needs, taking right into account aspects such as use frequency and ecological conditions. Carrying out a structured technique to set up upkeep makes it possible for operators to enhance efficiency and reduce the threat of unanticipated failures. Additionally, adhering to these intervals can boost safety and security criteria and boost overall efficiency. Eventually, well-planned maintenance timetables are essential in preserving the performance of product packaging tools and expanding its functional life-span, making sure a dependable production process.
Regular Assessment Practices
While equipment might seem operating well, regular evaluation practices are important for recognizing possible concerns before they influence production. These examinations must include a complete examination of critical parts, such as gears, sensors, and belts, to assure they run within specified parameters. Routinely examining for indications of wear, imbalance, or unusual sounds can help identify issues early. Furthermore, documenting examination findings can create an important history that assists in future troubleshooting. Operators ought to be trained to identify usual signs of breakdown, facilitating prompt treatment. Utilizing a methodical strategy to regular evaluations not just boosts tools dependability yet additionally reduces unexpected downtime, inevitably boosting general operational efficiency and performance.
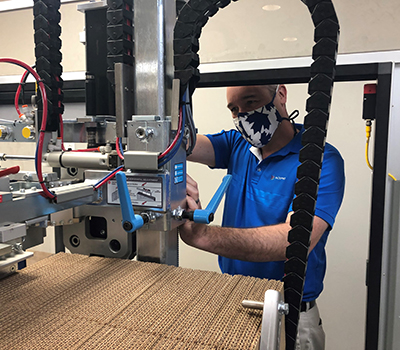
Lubrication and Cleansing Techniques
Regular assessments prepared for efficient upkeep, however lubrication and cleansing strategies play a crucial role in maintaining tools efficiency. Correct lubrication reduces rubbing between relocating parts, reducing damage while enhancing the efficiency of machinery. It is important to use the ideal type and amount of lubricating substance, as specified by the equipment manufacturer. Normal cleansing eliminates dirt, particles, and impurities that can hamper functionality, guaranteeing optimal procedure. Strategies such as utilizing soft brushes, pressed air, or vacuum cleaner systems can successfully maintain sanitation without harming sensitive parts. Packaging Equipment Repair Services. Developing a constant schedule for both lubrication and cleansing not only prolongs the tools's lifespan however additionally considerably lowers the chance of unforeseen failures, ultimately resulting in boosted efficiency in product packaging operations
Selecting the Right Fixing Company
How can a company guarantee it selects the most suitable product packaging equipment fixing provider? To make an educated option, business need to initially review the supplier's experience and credibility in the market. This can be achieved through on-line testimonials, endorsements, and referrals from other businesses.Next, examining the supplier's credentials and certifications is crucial, as these suggest a commitment to sector criteria and best practices. Additionally, organizations need to ask about the range of services provided, ensuring that the provider can deal with particular equipment issues.Cost is also a significant element; obtaining comprehensive quotes and understanding the rates structure will certainly aid avoid unforeseen costs. Lastly, timely reaction and availability for emergency situation repair work can greatly influence the decision, as equipment downtime can result in significant losses. By very carefully considering these factors, organizations can select a product packaging equipment look at this now repair service company that aligns with their operational needs.
The Repair Process: What to Expect
Cost Factors To Consider for Packaging Tools Repair Work
While the price of product packaging devices fixings can vary substantially based on numerous variables, recognizing these variables can aid businesses spending plan successfully. Crucial element influencing fixing prices consist of the type of equipment, the level of the damages, and the schedule of replacement components. For example, specialized or older devices may need extra pricey parts, driving up prices. Labor prices also play a considerable duty; technicians with customized expertise may bill higher costs. Additionally, the necessity of the repair service can affect rates, as expedited solutions generally sustain added charges. Businesses should likewise take into consideration the possible downtime related to repairs, which can result in shed income. By assessing these elements, firms can produce a much more accurate monetary prepare for maintenance and repair work, guaranteeing they designate adequate resources while minimizing unanticipated expenditures. Recognizing the total price of ownership is necessary for reliable budgeting and lasting operational efficiency.
Tips for Prolonging the Lifespan of Your Equipment
To make the most of the lifespan of product packaging machinery, businesses need to carry out an aggressive maintenance strategy that consists of regular examinations and timely servicing. Arranged exams can aid determine small issues before they intensify, stopping expensive repair work and downtime. Appropriate training for drivers is additionally necessary; well-informed staff can identify very early indicators of wear and immediately address them.Additionally, keeping machinery tidy and complimentary from debris guarantees peak performance and reduces wear on parts. Adhering to and making use of high-quality lubricating substances manufacturer guidelines for parts replacement can even more boost durability. Businesses should likewise keep an accurate log of maintenance tasks, which aids in tracking performance patterns and organizing future services.Finally, buying high quality replacement parts as opposed to selecting cheaper alternatives can significantly impact machinery longevity. By following these suggestions, business can foster an extra reputable and reliable manufacturing environment, eventually prolonging the life-span of their product packaging tools.
Regularly Asked Concerns
How Frequently Should I Set Up Repairs for My Devices?
The frequency of arranged fixings for equipment depends upon use, maker referrals, and upkeep background. Positive approaches and regular evaluations can help figure out perfect intervals, making certain effectiveness and minimizing unexpected failures for long life.
Can I Do Repairs Myself, or Should I Hire an Expert?
The individual contemplated whether to carry out repair services individually or engage a specialist. While some minor repairs could be manageable, complicated issues normally require customized abilities and tools, making professional aid the more secure and a lot more efficient option.
What Warranties Are Readily Available for Repair Service Providers?
Different warranties for repair services exist, frequently covering parts and labor for particular periods. Customers must inquire about solution guarantees, as reputable suppliers usually use guarantees to guarantee top quality and client contentment in their fixings.
Exactly how Do I Select the Right Parts for My Equipment?
Picking the best components for equipment entails wikipedia reference reviewing compatibility, top quality requirements, and producer specs. Investigating reputable providers and seeking advice from with experts can likewise assure peak efficiency and long life of the tools in concern.
What Certifications Should a Repair Work Professional Have?
When taking into consideration accreditations for a fixing service technician, one should focus on industry-standard credentials, such as those from the National Institute for Accreditation in Engineering Technologies, in addition to particular producer training to ensure knowledge in appropriate devices. Product packaging devices repair service solutions play a crucial role in the manufacturing procedure. Several firms focus on purchasing new packaging equipment, understanding the significance of repair services is vital for preserving operational effectiveness (Packaging Equipment Repair Services). Recognizing the signs that product packaging tools requires repair work is crucial for preserving functional performance. Reduced manufacturing effectiveness typically indicates that packaging equipment needs fixing. Just how can a company assurance it picks the most ideal packaging equipment repair work solution copyright?